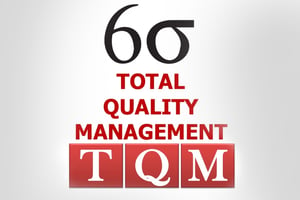
Six Sigma and total quality management (TQM) are both methods of process improvement, with enough similarity between the two that deciding which to use may be difficult. They are both highly effective systems for eliminating waste and preventing errors, but there are key differences to keep in mind.
What Is Six Sigma?
First introduced by a Motorola engineer named Bill Smith in the 1980s, Six Sigma is a relatively recent development. It’s an offshoot of TQM, though, not a replacement for it. Six Sigma’s focus is on quantitative measurements and statistical analysis.
Typical uses of Six Sigma
Six Sigma’s roots in statistics are evident in its name. The Greek letter sigma is used to represent one standard deviation on a bell curve. This ties into its manufacturing origins as well. When a process has achieved six sigma, that means something will need to be six standard deviations from the mean to count as a defect. That comes out to about 3.4 defects per one million items produced.
Six Sigma’s uses have transformed and expanded beyond manufacturing, however. Today, it is used across industries for everything from improving customer retention rates to better understanding demand in a dynamic environment. Six Sigma holds that any business process can be quantified, and those numbers can be used to strive for continuous improvement.
Six Sigma certifications
The Six Sigma system is divided into different belt levels based on training, exams, and position within an organization. The belt levels are:
- White Belt: A basic look at the fundamental aspects of Six Sigma
- Yellow Belt: A more in-depth look at some of the specifics, including how to begin applying it in a professional setting
- Green Belt: At this level, there’s a focus on problem-solving, analysis, and project management
- Black Belt: An increased focus on leadership in addition to mastery of Six Sigma concepts
- Master Black Belt: Additional leadership and mentorship responsibilities and an expert level of knowledge about Six Sigma philosophies
In addition to the Six Sigma belt levels, there are also different certifying organizations. No one unified standard exists, so certifications can be earned from various universities and organizations, like the American Society for Quality or the International Association for Six Sigma Certification, or in-house within a company.
Pros and cons of Six Sigma
As with anything, Six Sigma has its pros and cons, not all of which are present in every circumstance.
Pros:
- Improves processes and customer satisfaction
- Reduces waste and unnecessary expenses
- Requires different certification levels for different needs
Cons:
- Data analysis can be complicated and time-consuming
- Multiple standards using the same vocabulary can lead to confusion
- The implementation may be costly
What Is Total Quality Management?
TQM is a much older concept than Six Sigma. It began to take shape at the same time as modern quality control practices with the publication of Economic Control of Quality of Manufactured by William A. Shewhart. Its focus is on improving output quality, typically as defined by customer views, whether those outputs are goods or services.
Typical uses of total quality management
TQM is used to improve customer experience by improving processes within a company. Improvements might take the form of supply chain changes that allow customers to get their goods more quickly or additional training for employees to ensure customers can be assisted at the highest possible level.
Unlike Six Sigma, success is not determined by objective data. Instead, it’s based on customer perception. Let’s say customers are unhappy with shipping delays on online orders. If a warehouse reorganization project leads to customers receiving their orders eight percent faster, but the customers aren’t satisfied, the reorganization was a failure by TQM standards.
Setting employees up for success is a critical part of TQM. Well-trained employees with adequate resources are best-able to meet or exceed customer expectations. Additionally, employees who feel supported in their roles are more likely to stay engaged and less likely to leave in search of a new position, preventing the loss of knowledge and experience.
Total quality management certifications
Like Six Sigma, TQM lacks a single, nationally or internationally-recognized certifying body. But unlike Six Sigma, there aren’t clear leaders who hold a significant portion of the market share. This is because TQM draws heavily on industry and company-specific standards. It’s a highly tailored approach to organizational management, making a one-size-fits-all approach to certification impossible.
Companies may offer an internal certification program, and the principles of TQM are covered in many more broadly focused management courses. When looking for a management class or certificate program, look for one that covers:
- Communication and leadership skills
- Research and survey design
- Data analysis, ideally with a focus on qualitative data
- Process and workflow design and visualization
- Quality management systems
Depending on industry standards and requirements, it may be helpful to pair a management course with another industry-specific course or certification.
Pros and cons of total quality management
TQM would not have had such a lasting impact on organizational management if it didn’t come with significant benefits, but it has drawbacks as well.
Pros:
- Highly customizable for a range of industries
- Can reduce wasted time and money
- Potential for increased customer satisfaction
Cons:
- No consensus on what TQM is outside of its basic concepts
- Requires buy-in from the entire company to implement successfully
- Can be costly in terms of financial and time investments when first getting started
Which Is Right for You?
Unfortunately, there’s no easy answer as to which is better or even best for you. Both Six Sigma and TQM have helped companies across industries transform their processes in the past. Your team or company could likely benefit from aspects of them both, but there are a few general guidelines.
Industries such as food service, hospitality, and technical support may benefit more from TQM than Six Sigma because employees are working closely with individual customers. Negative customer input in industries like these can have a near-immediate effect on business in the form of online reviews and word-of-mouth, so it makes sense to center customer experience.
Manufacturing, agriculture, and other industries where a product is being created with only indirect customer contact may benefit more from Six Sigma. Improving efficiency based on time, money, and materials saved is likely to be more productive for these industries than looking at customer experience.